Industrial Services: the heart of petrochemical plants
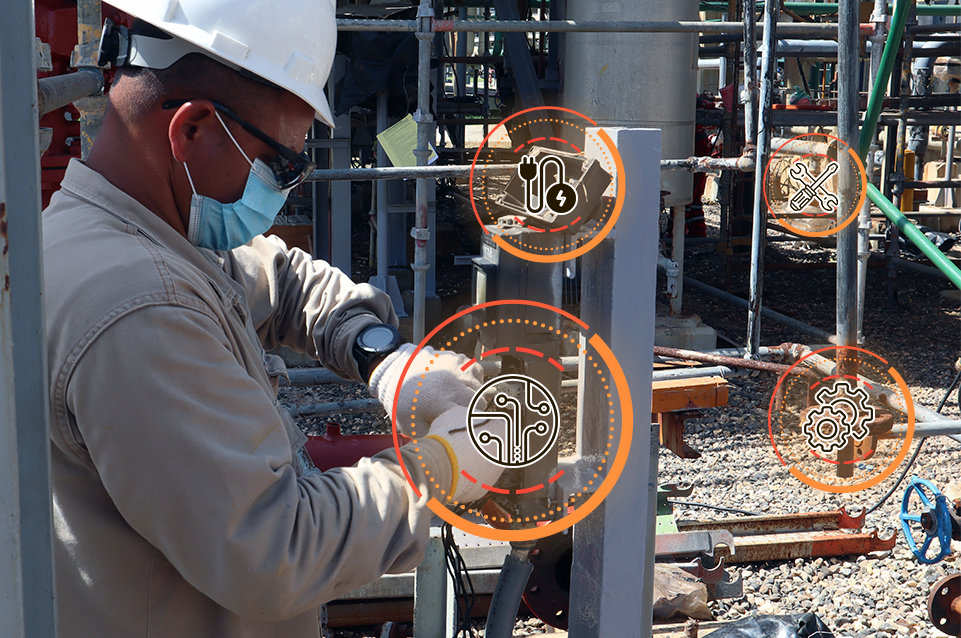
Through RCM, improvements in equipment reliability and plant performance can be achieved.
Reliability Centered Maintenance, also known as RCM (Reliability Centered Maintenance) is a methodology used in the preparation of maintenance plans, which is derived from reliability engineering and which seeks to reduce the probability of failure of the assets of an industrial plant. .
For Jesús García, Director of Operations at Corporación B&D, reliability engineering is a fundamental pillar in any production process, because it guarantees the availability of a plant. “In our case, we have developed and implemented reliability engineering tools, such as RCM, this has allowed us to analyze recurring failures that may be present in a system.”
RCM Benefits
- Decreased maintenance costs.
- Increased production.
- Reduces delays in work orders.
- Improves team control.
- Maximize maintenance operations.
- Less dependence on the manufacturer.
However, this methodology does not provide an instant solution to all maintenance problems in a plant, it is a technique that if you know how to use it gives good results; This is where experience and knowledge play an important role in the implementation of this type of tool.
García explains that when implementing this type of methodology it is necessary to collect all the information on the asset such as manuals, plans, know the operational context, conduct interviews with production and maintenance personnel to find out what problems are occurring, all of this. based on international regulations. “For example, the collection and structuring of maintenance and reliability data is carried out in accordance with ISO 14224, which, although it is aimed at the oil, petrochemical and natural gas industry, can be adapted for application in any industry. that has physical assets in the processes”.